Come si producono gli scarponi in fibra di carbonio
Come raccontato nella visita allo stabilimento produttivo de La Sportiva di Ziano di Fiemme, l’azienda trentina è entrata di prepotenza nel mercato degli scarponi da scialpinismo con un modello in fibra di carbonio… e per i modelli top di gamma si è scelto di continuare su questa strada.
La volontà di proseguire su questo materiale è testimoniata dall’arrivo in fabbrica di un’autoclave appositamente dedicata alla sperimentazione e produzione di componenti in fibra di carbonio. Luca Mich assieme ad un assistente del reparto “ricerca e sviluppo” mi hanno accompagnato in quest’area dell’azienda staccata dallo stabilimento principale in cui la ricerca tecnologica e l’innovazione dei materiali si presentano nella forma più alta.
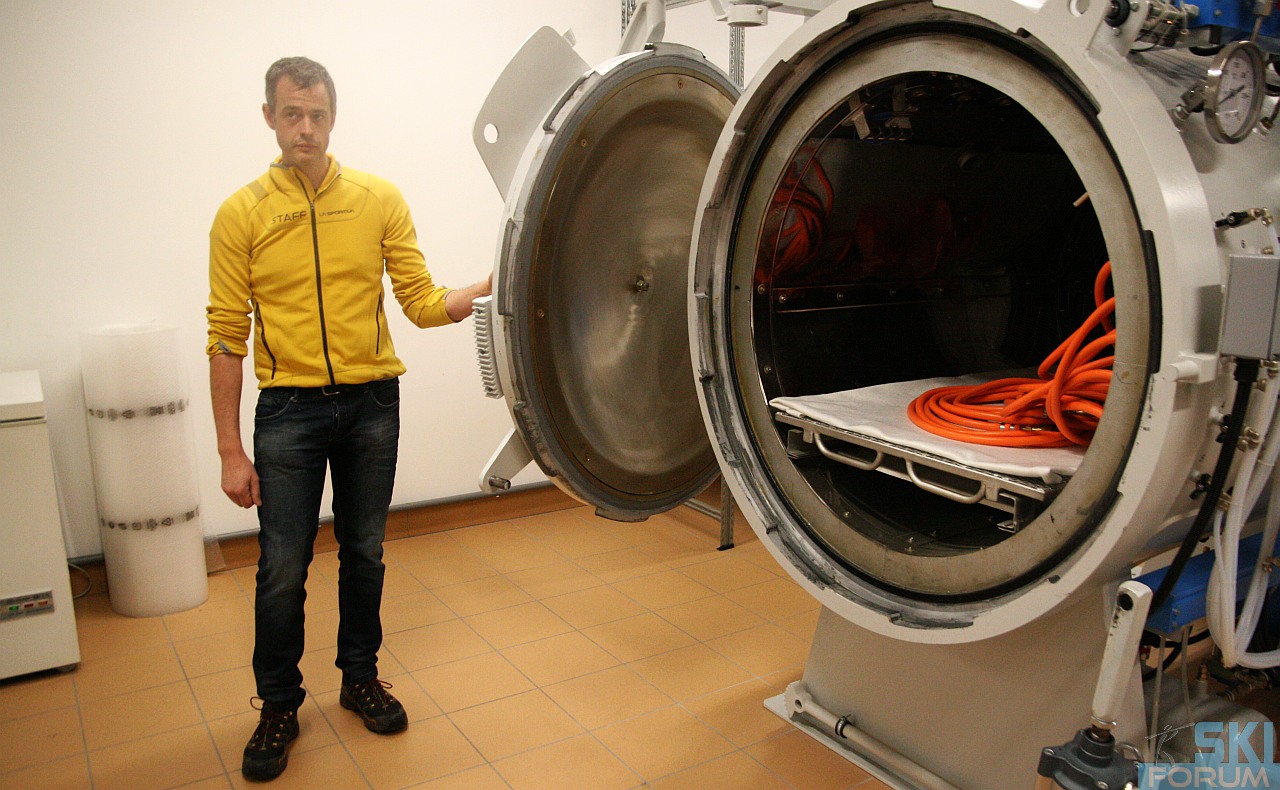
I componenti in fibra di carbonio presentano alcuni indubbi vantaggi: primo fra tutti – pensando al settore delle competizioni e prestazioni – la leggerezza, secondo, la rigidezza che può essere fornita al manufatto preferendo alcune direzioni piuttosto che altre. L’unione di questi due fattori consente la realizzazione di componenti ideali per prodotti “top di gamma”.
È facile però immaginare il rovescio della medaglia: il costo. Produrre un pezzo in fibra di carbonio richiede non solo molto tempo, ma anche una conoscenza approfondita del processo. Ed inoltre per componenti con forme complicate come quelle tipiche degli scarponi da sci, il processo non si può automatizzare.
Grazie al gentile assistente ho potuto vedere come viene creato un componente in fibra di carbonio dalla A alla Z. Mi preme evidenziare subito un aspetto: quello che chiamiamo fibra di carbonio è in realtà una somma di strati di fibre pressate ed incollate tra di loro (ogni strato si chiama layer).
La prima scelta da fare riguarda il tessuto in fibra di carbonio di partenza. Ciò che cambia tra un tessuto ed un altro riguarda la qualità del materiale, lo spessore delle fibre e soprattutto la tessitura del cosiddetto “panno in fibra”. Nella foto seguente si può vedere uno dei classici “panni di fibra” così come arrivano in azienda; la tessitura in questo caso è composta da fibra disposte a 90 gradi.
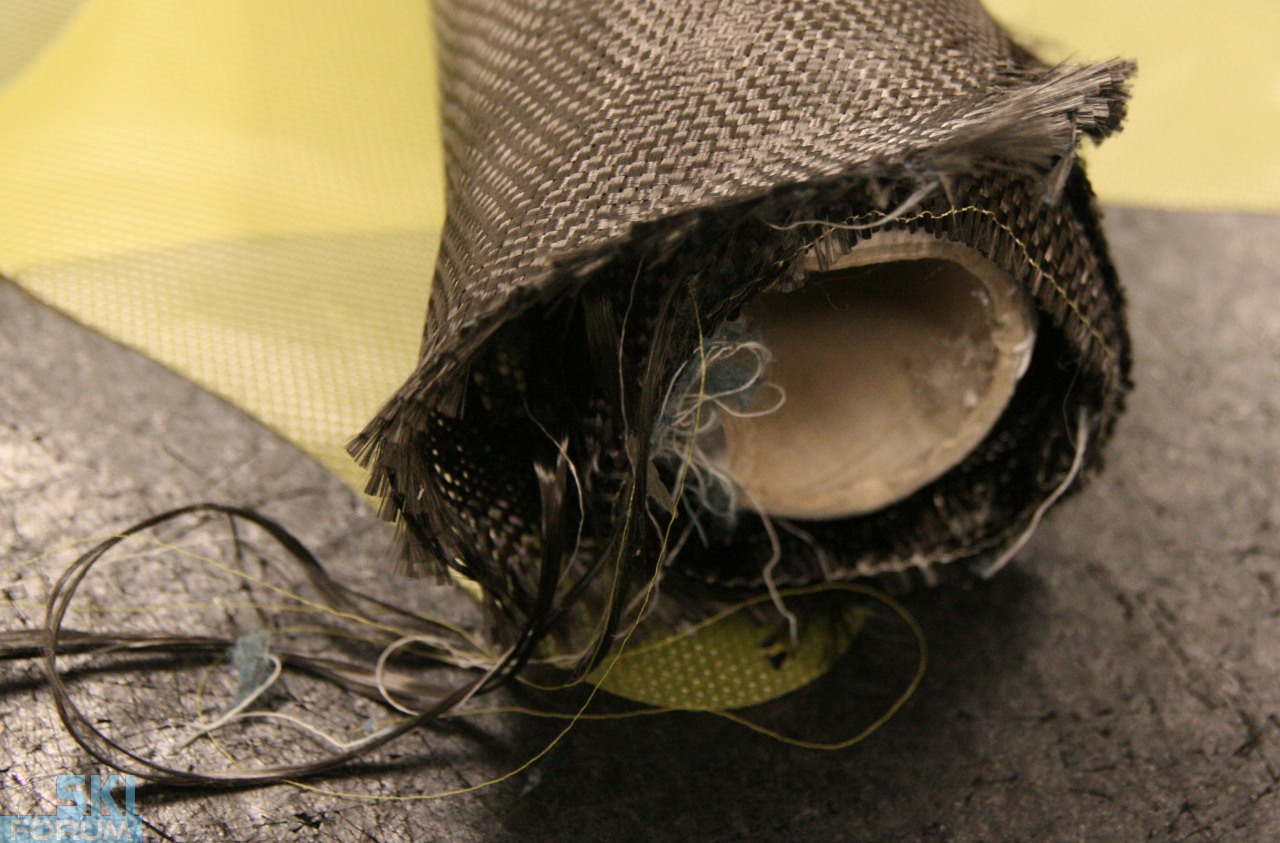
Questo parametro, la tessitura/intrecciatura, è quello che andrà a decidere le caratteristiche meccaniche del manufatto. Il comportamento della fibra di carbonio è fortemente anisotropo, una difficile parola tecnica per esprimere semplicemente che la resistenza meccanica cambia in funzione della direzione.
Un pannello di fibra avente la tessitura incrociata a 45 o 90 gradi avrà resistenze più o meno simili lungo tutte le direzioni, mentre uno con tessitura avente le fibre orientate in prevalenza lungo una stessa direzione avrà comportamento meccanico diverso a seconda della direzione in cui viene caricato (comportamento anisotropo).
Da questa premessa deriva la seconda scelta da fare per realizzare un pezzo in fibra di carbonio: il pacchetto di fibre da usare. È molto importante scegliere la giusta sequenza dei layer, sequenza che varia in funzione delle caratteristiche che si vogliono privilegiare.
Nella foto seguente si vede il “pacchetto” di panni in fibra per un gambetto di uno scarpone da sci.
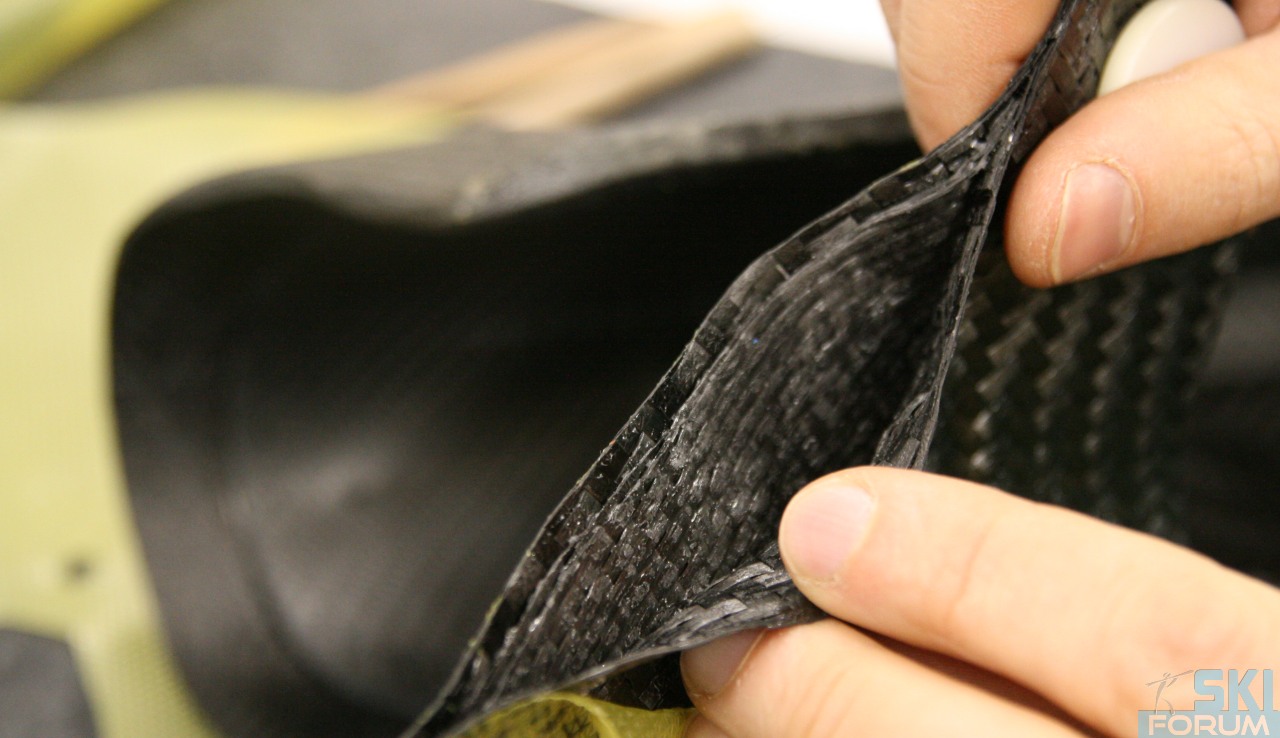
Nella foto seguente si vede il “libretto – ricetta” per costruire un gambale. All’interno di quei fogli è riassunto il lavoro di mesi e mesi di sperimentazione e di decine e decine di prototipi. In quella manciata di pagine viene descritto il modo in cui preparare il “multi-layer” di fibre di carbonio: viene specificato il tipo fibra, la tessitura e l’ordine con cui formare il “panino” da porre in autoclave per il processo di cristallizzazione.
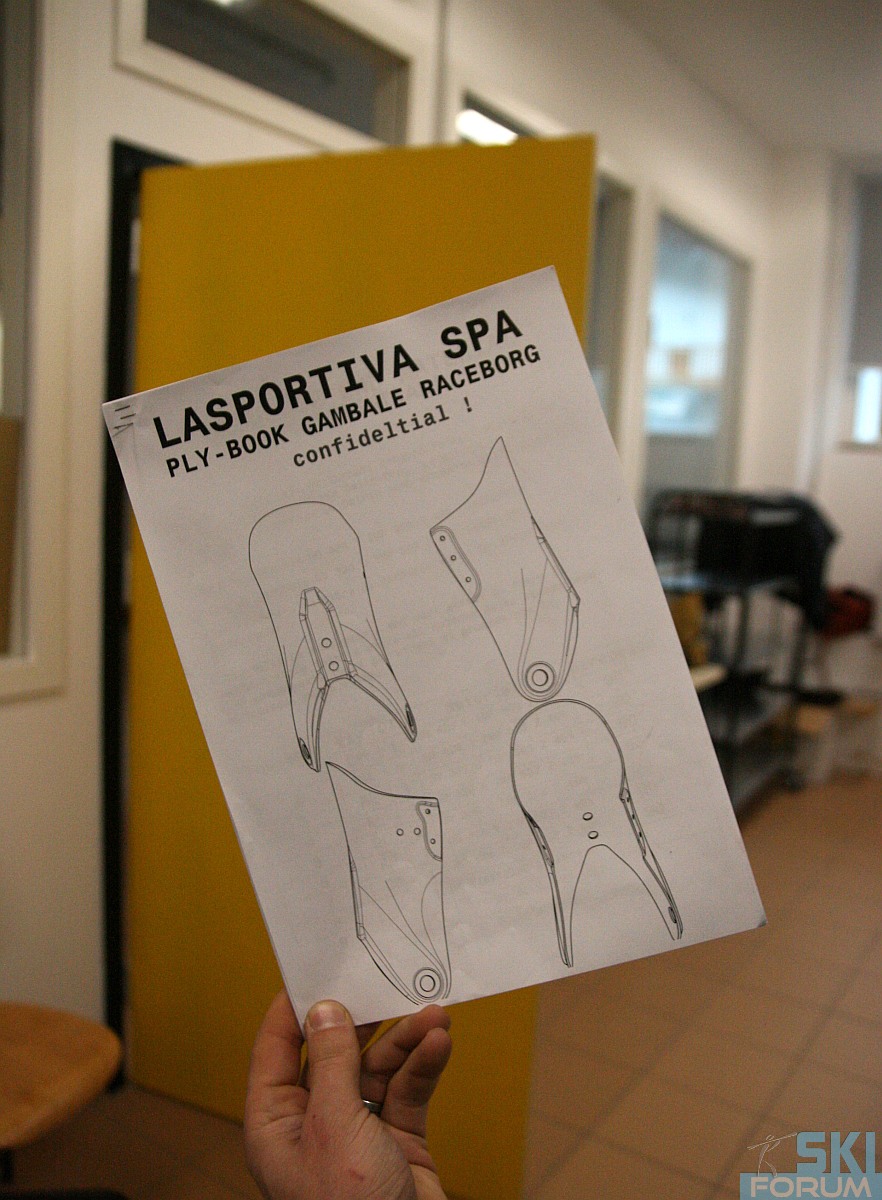
Le fibre di carbonio sono tenute assieme da una resina che nella fase di preparazione si trova nello stato liquido mentre nel prodotto finale è solida ed ha il compito di tenere uniti gli strati di fibra consentendo loro di trasmettersi gli sforzi l’uno con l’altro.
Il processo che fa passare la resina dallo stato liquido a quello solido avviene in un’autoclave nella quale viene creato il sottovuoto: questo è il processo più delicato.
Al fine di garantire una trasmissione delle forze meccaniche il più omogenea possibile tra gli strati di fibra di carbonio durante il processo di cristallizzazione della resina è importantissimo che i vari layer siano il quanto più possibile compressi uno contro l’altro. È inoltre necessario che non rimanga aria all’interno del “pacchetto” di strati. Questo obiettivo si raggiunge creando un’atmosfera in depressione – il sottovuoto – tra il componente da produrre ed un ambiente esterno.
Nella foto seguente si vede la preparazione di un gambale. All’interno del sacco rosso si sta creando il sottovuoto.
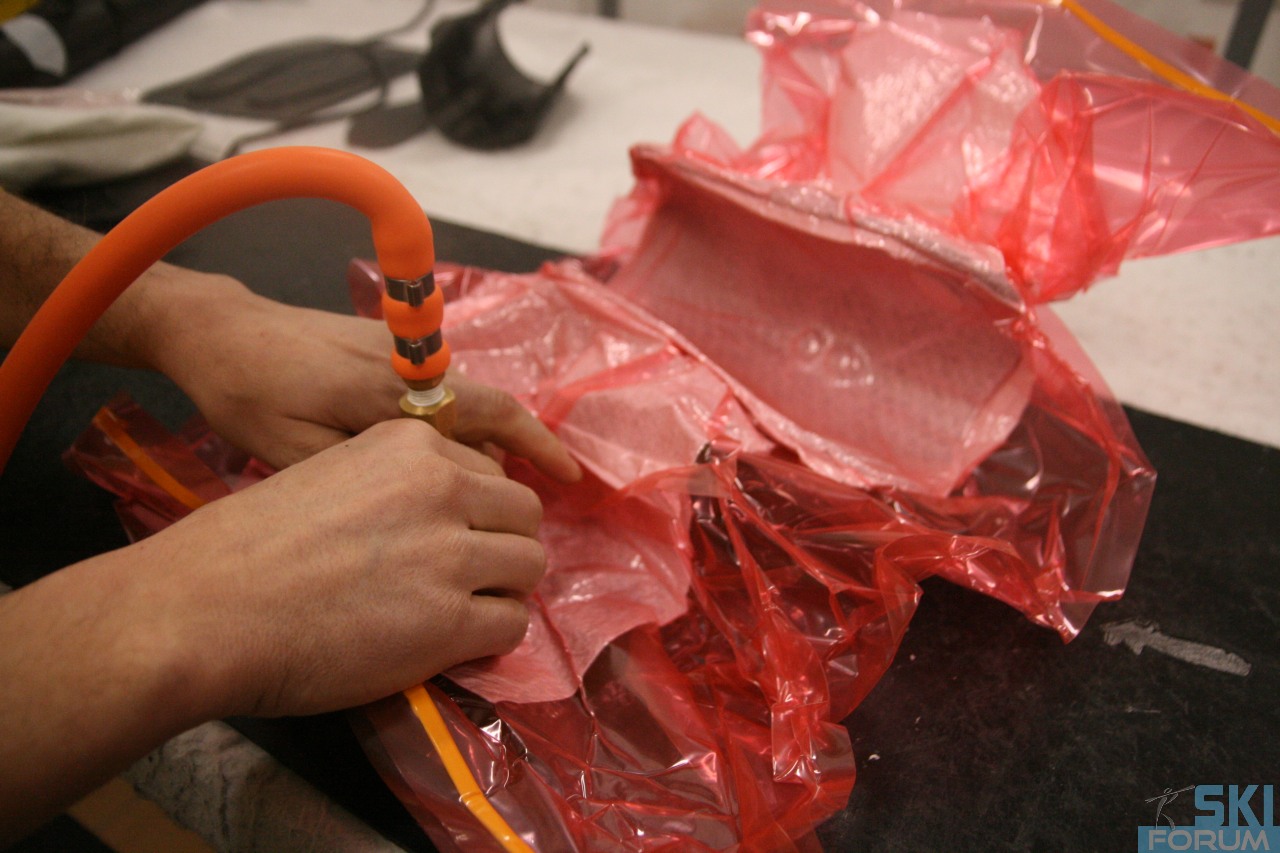
Il pacchetto di layer di fibra di carbonio viene adagiato ad uno stampo il quale darà la forma finale del manufatto. Sarà la differenza di pressione a premere le fibre contro di esso andando a replicare la forma del componente da produrre. Una volta che il tutto è pronto, si accende l’autoclave ed in essa si completa il processo di solidificazione.
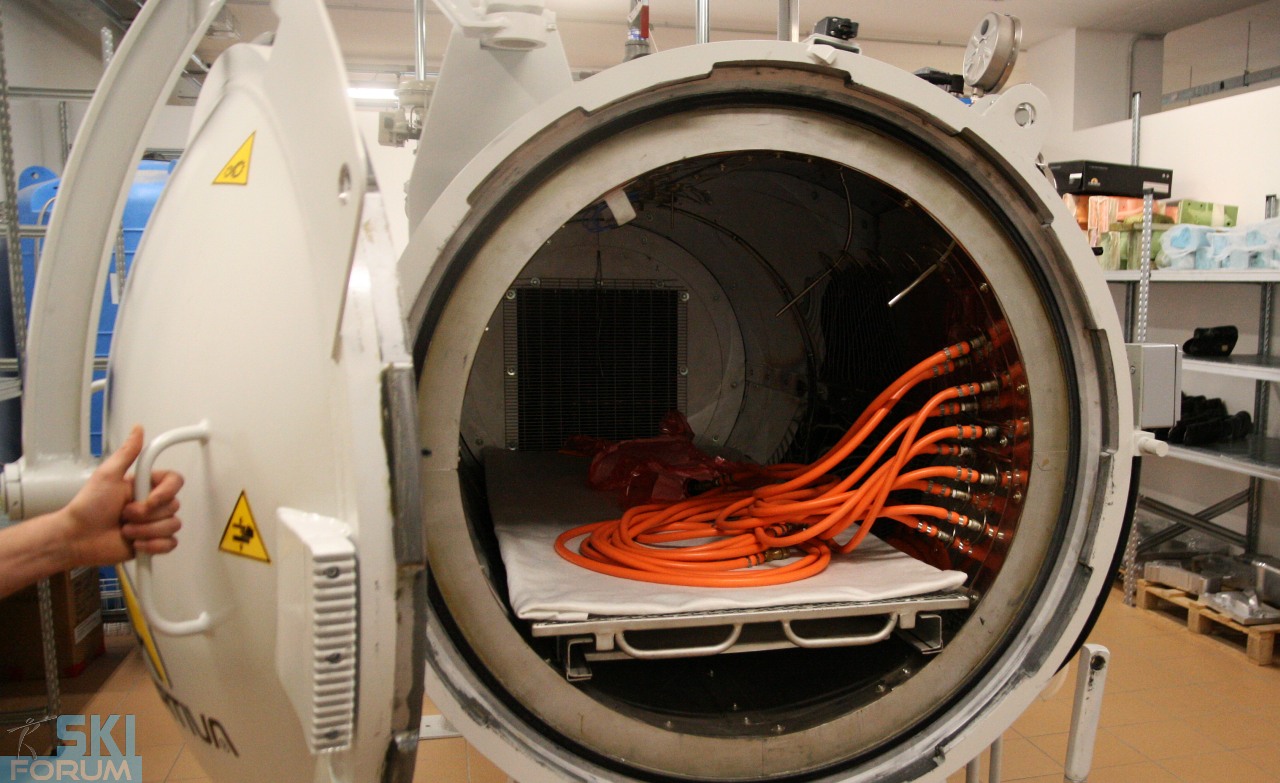
La temperatura viene fatta variare secondo un ciclo ben preciso. Dapprima si fa aumentare leggermente comportando una liquefazione della resina che diventa molto più fluida e meno viscosa. In questo modo essa va a “bagnare” tutta la superficie degli strati di fibra di carbonio.
Quando le fibre sono ben “imbevute” di resina la temperatura viene fatta aumentare ulteriormente. A questo punto le molecole della resina cristallizzano ed il tutto si solidifica: il manufatto è pronto!
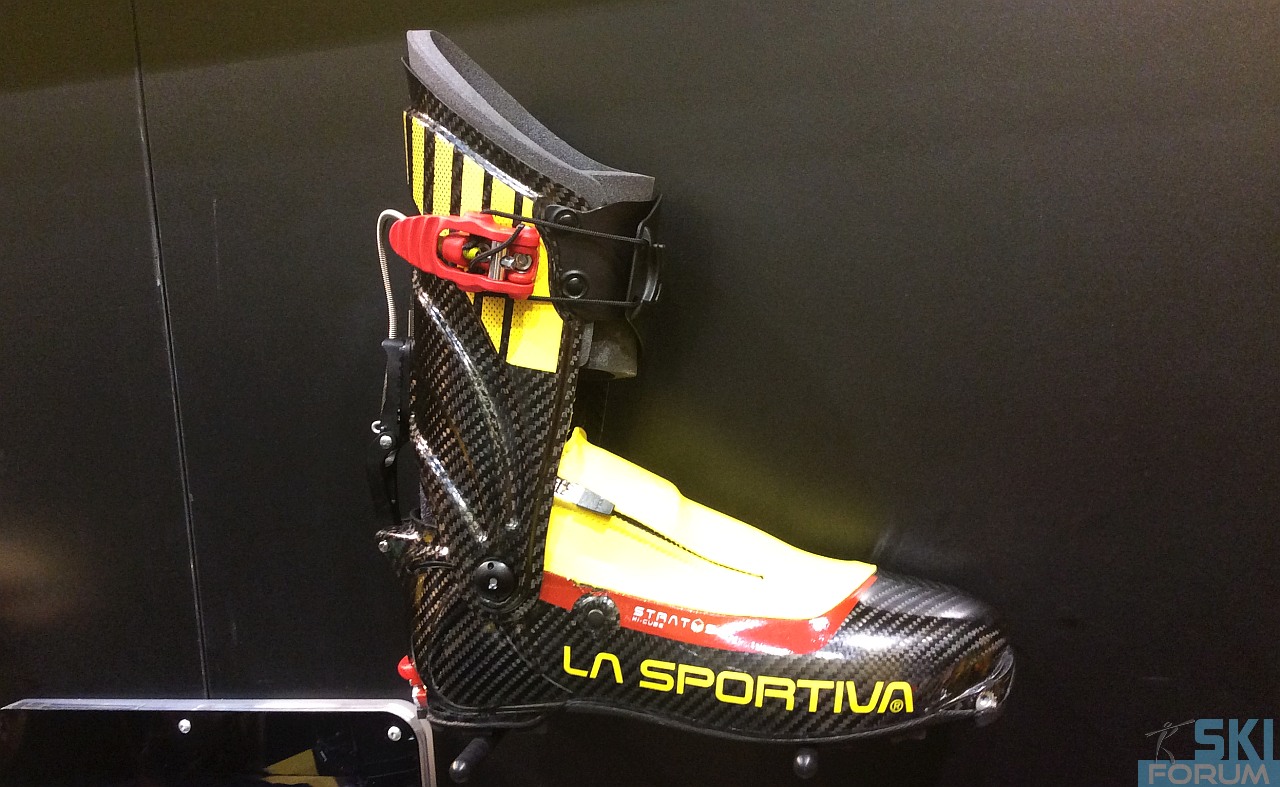


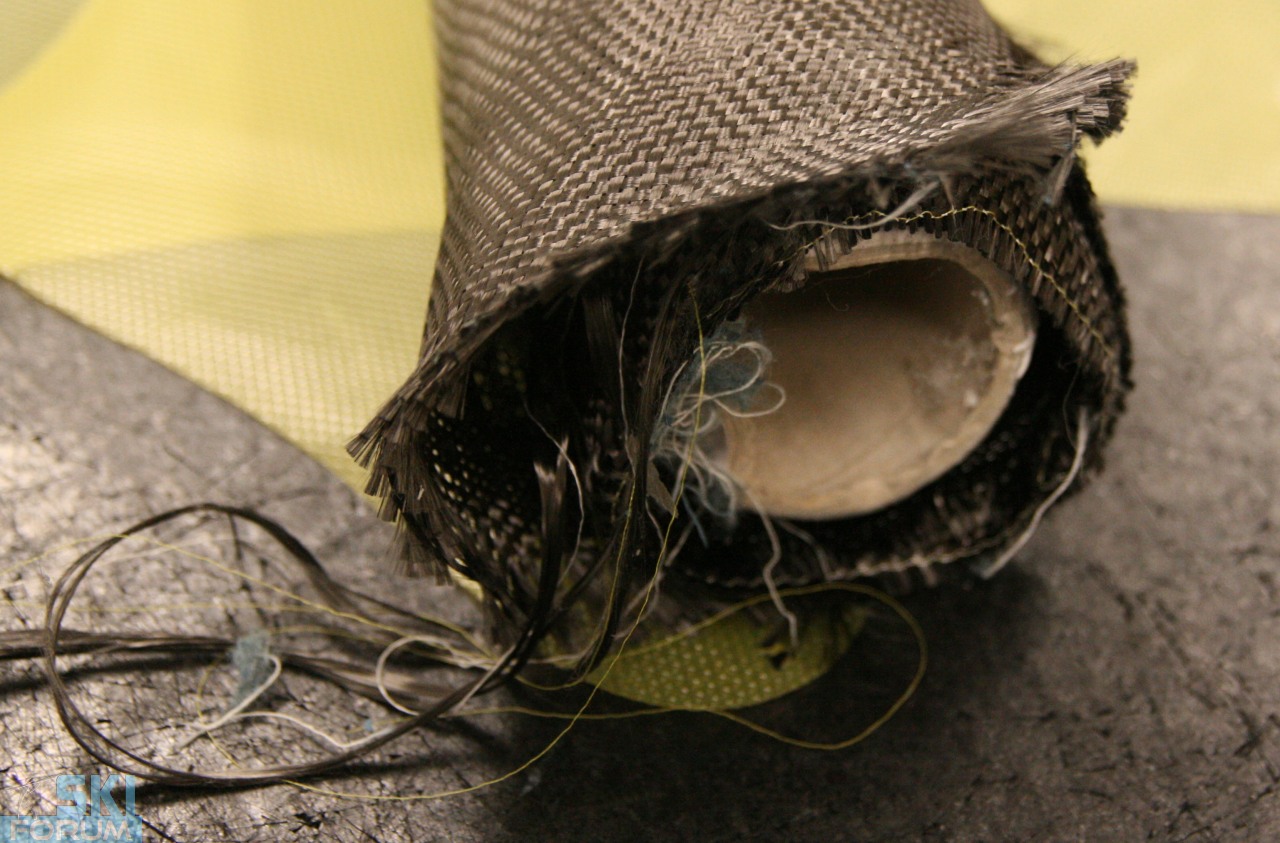
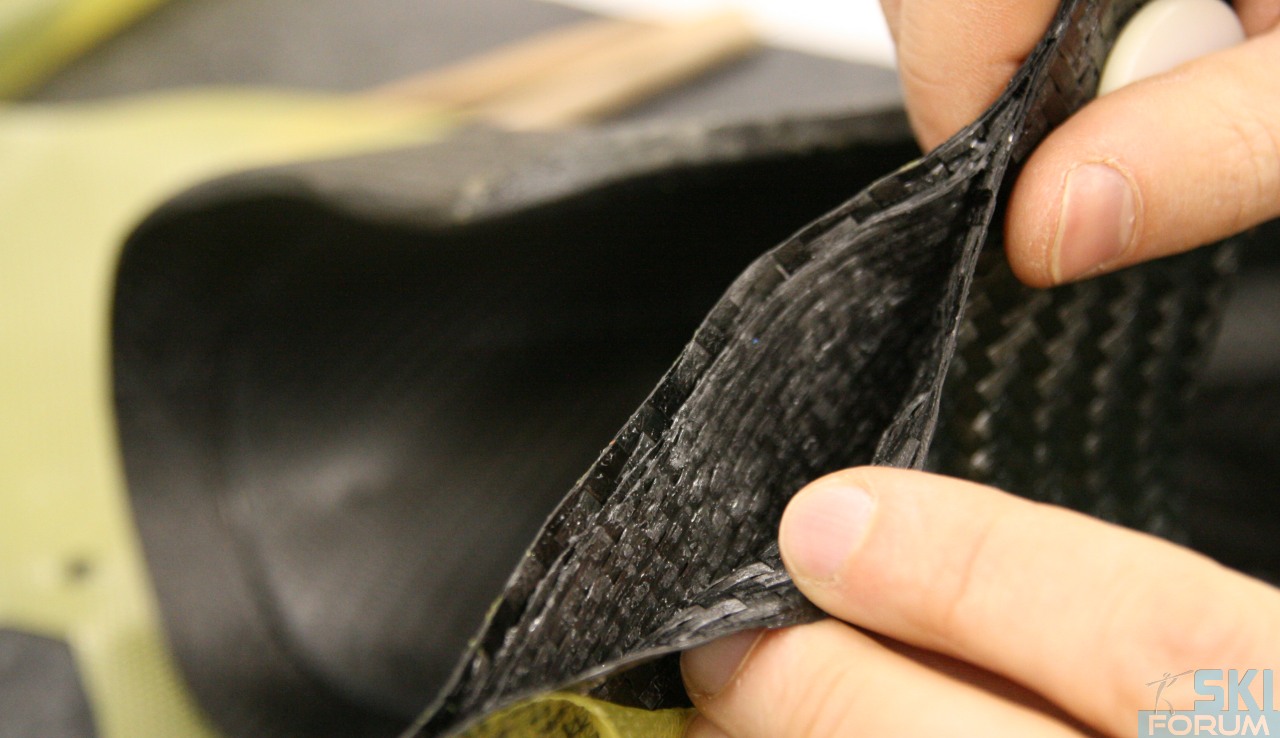


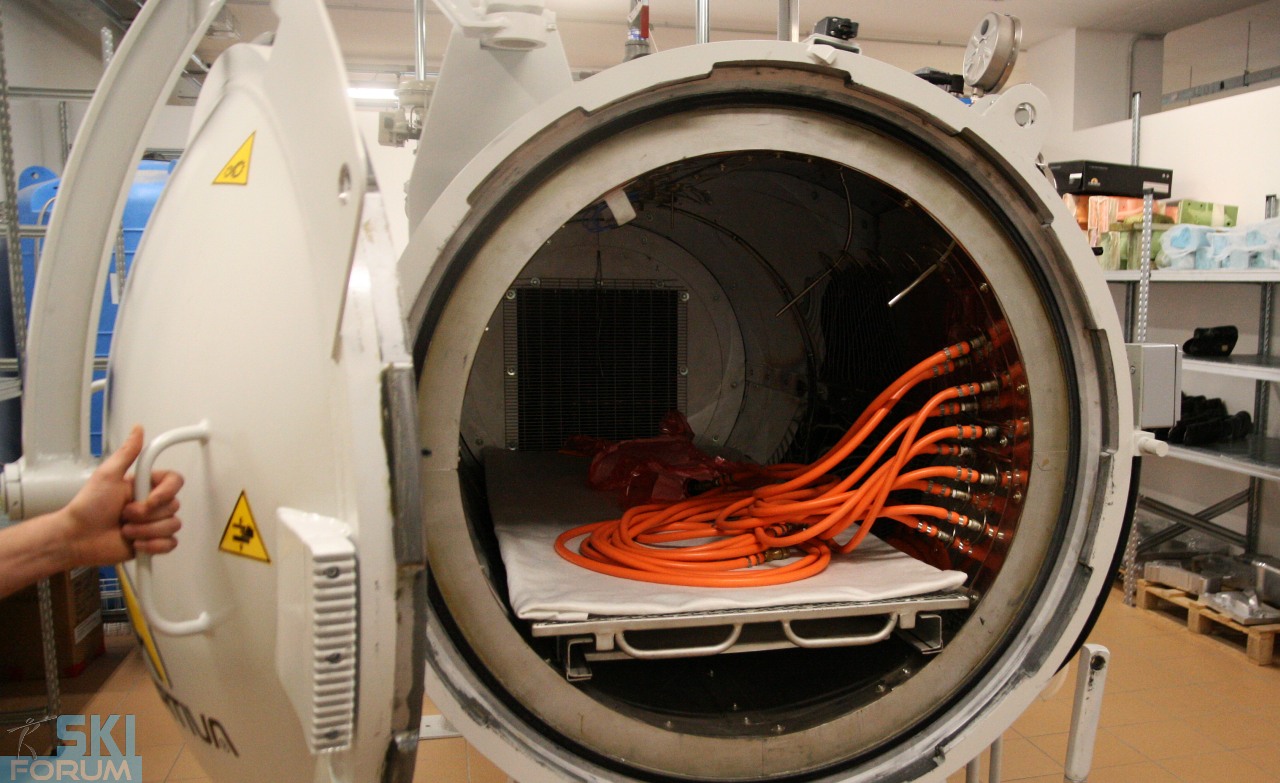

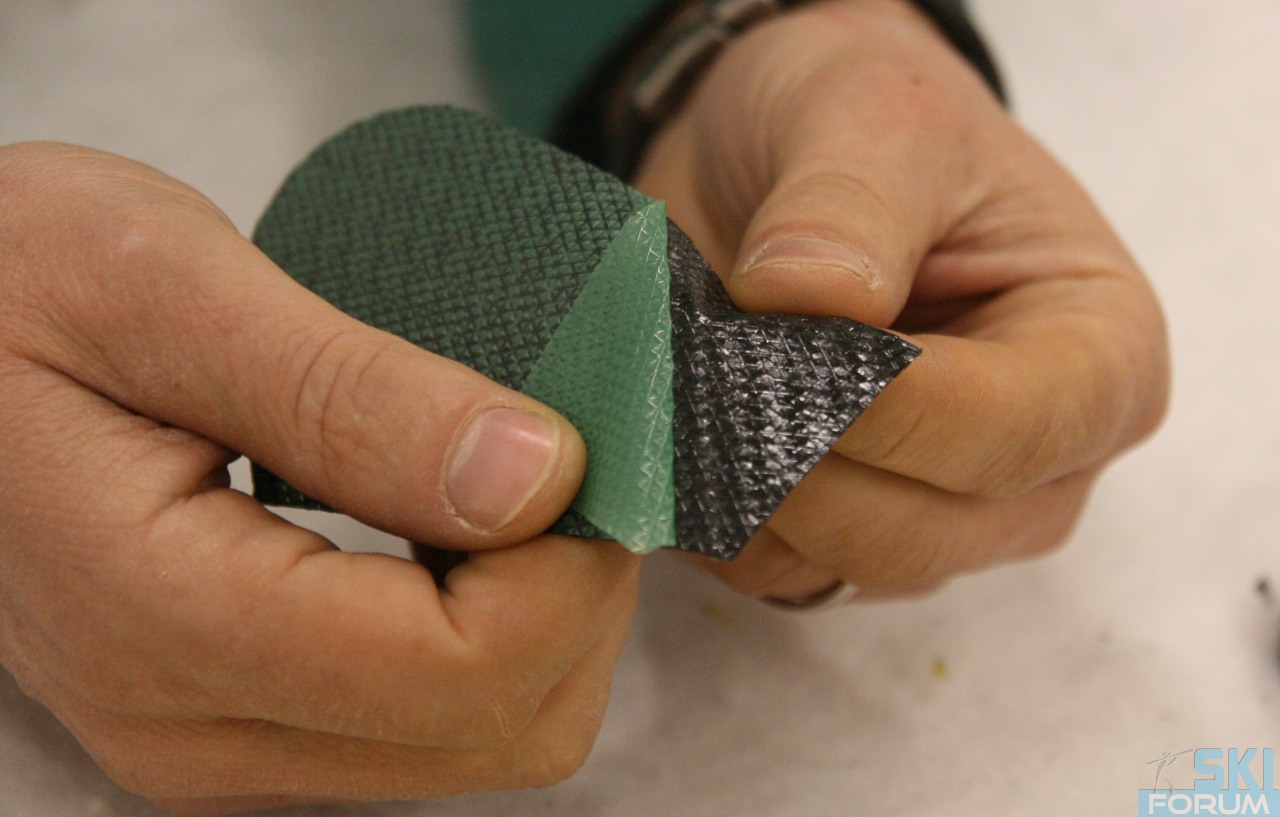
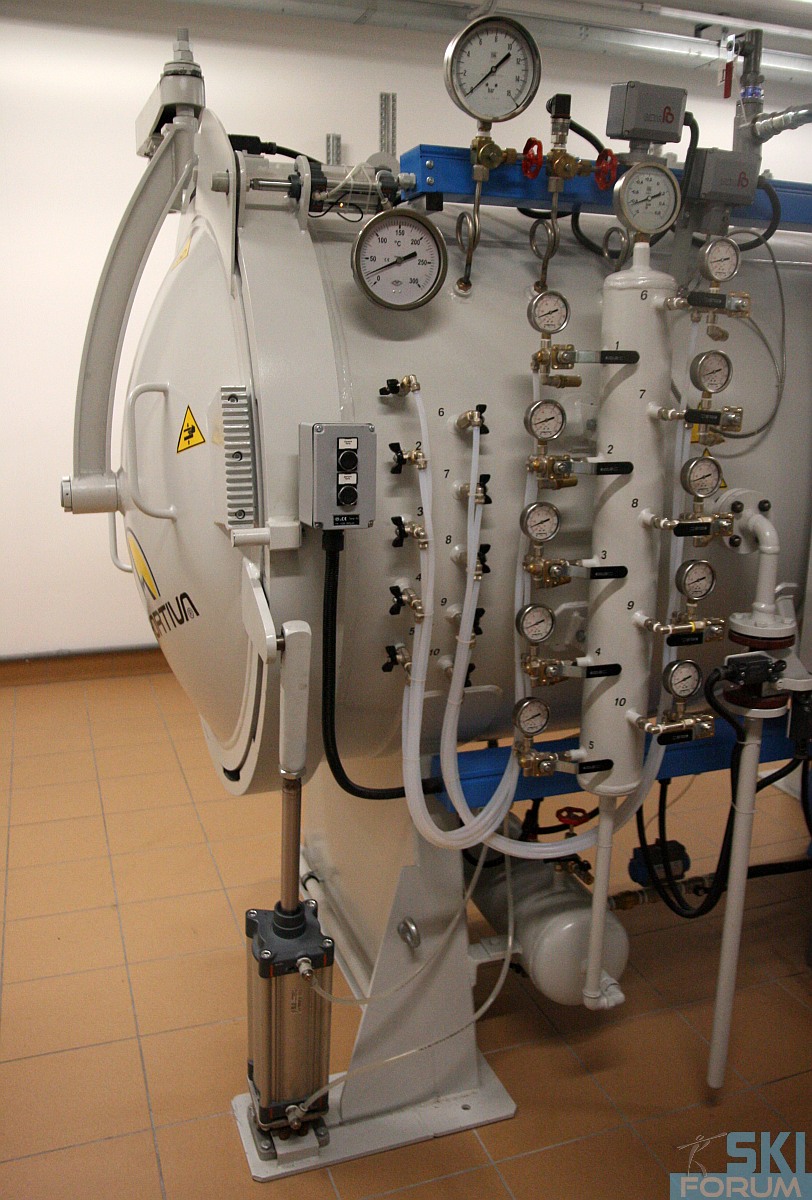

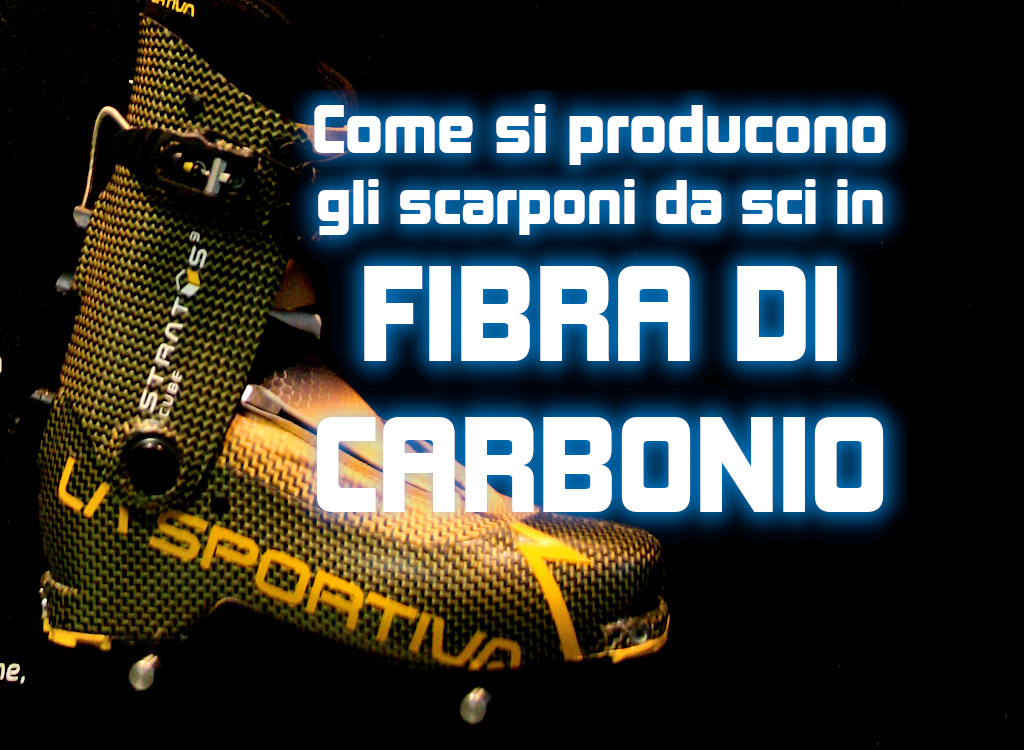
articolo scritto da Fabio Disconzi per SkiForum